QR код
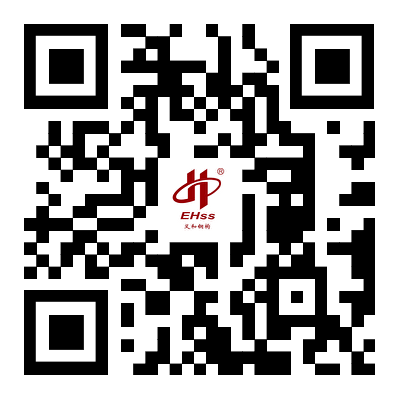
Продукти
Свържете се с нас
Телефон
Електронна поща
Адрес
№ 568, първокласен път на Янкинг, High-Tech Zone Jimo, град Qingdao, провинция Шандонг, Китай
Инженерна сграда от стоманена конструкцияе известен като зеления проект на 21-ви век, стоманената конструкция има много предимства като висока якост, голяма товароносимост, леко тегло, малък обем на заеманото пространство, лесно производство и монтаж на компоненти, спестяване на дървесина и т.н., така че е все по-широко използвани в промишлени и граждански сгради. Сградите със стоманени рамки и складовете със стоманени конструкции са навсякъде.
С бързото развитие на промишлеността, устойчивостта на корозия на стоманата и слабата устойчивост на ръжда и корозия и други проблеми постепенно се появиха, особено в крайбрежните райони и химическата промишленост се превърна в важен проблем!
Корозията на стоманената конструкция не само причинява икономически загуби, но също така носи скрита опасност за безопасността на конструкцията, а инженерните аварии, причинени от корозия на стомана, са често срещани, така че антикорозионната обработка на стоманената конструкция (особено тънкостенните стоманени компоненти) е с голямо икономическо и социално значение, а по-долу са някои въведения и дискусии относно проблемите, открити в процеса на строителство и някои методи за лечение.
1. Основни причини за корозия на стоманени конструкции
Предотвратяването на корозията на стоманата започва с разбирането на причините за корозията на стоманата.
1.1 Механизъм на корозия на стомана при стайна температура (под 100°C)
Корозията на стоманата при стайна температура е основно електрохимична корозия. Стоманените конструкции се използват в атмосферата при стайна температура, като стоманата е корозирала от действието на влага, кислород и други замърсители (непочистена заваръчна шлака, слой ръжда, повърхностна мръсотия) в атмосферата. Относителната влажност на атмосферата е под 60%, корозията на стоманата е много слаба; но когато относителната влажност се увеличи до определена стойност, скоростта на корозия на стоманата внезапно се повишава и тази стойност се нарича критична влажност. При стайна температура общата критична влажност на стоманата е от 60% до 70%.
Когато въздухът е замърсен или има сол във въздуха в крайбрежните райони, критичната влажност е много ниска, стоманената повърхност лесно се образува воден филм. По това време, заваръчна шлака и необработен слой ръжда (железен оксид) като катод, компоненти на стоманена конструкция (основен материал) като анод във водния филм електрохимична корозия. Атмосферната влага, адсорбирана върху стоманената повърхност за образуване на воден филм, е определящият фактор за корозията на стоманата; относителната влажност на атмосферата и съдържанието на замърсители са важни фактори, влияещи върху степента на атмосферна корозия.
1.2 Корозионен механизъм на стомана при висока температура (над 100 ℃)
Корозията на стоманата при високи температури е предимно химическа корозия. При висока температура водата съществува в газообразно състояние, електрохимичният ефект е много малък, сведен до вторичен фактор. Контактът на метал и сух газ (като O2, H2S, SO2, Cl2 и др.), повърхностното генериране на съответните съединения (хлориди, сулфиди, оксиди), образуването на химическа корозия на стоманата.
2 Методи за защита от корозия на стоманени конструкции
Според електрохимичния принцип на корозията на стоманата, докато образуването на корозионна батерия е предотвратено или унищожено или катодните и анодните процеси са силно блокирани, корозията на стоманата може да бъде предотвратена. Използването на метод на защитен слой за предотвратяване на корозия на стоманена конструкция е често срещан метод в момента, често използваният защитен слой има следните видове:
2.1 Метален защитен слой: метален защитен слой е метал или сплав с катоден или аноден защитен ефект, чрез галванопластика, напръскване, химическо покритие, горещо покритие и просмукване и други методи, необходимостта от защита на металната повърхност за образуване на метален защитен слой (филм) за изолиране на метала от корозивната среда в контакт с корозивната среда или използването на електрохимичен защитен ефект на метална защита, така че да се предотврати корозия.
2.2 Защитен слой: чрез химични или електрохимични методи да се направи стоманената повърхност да генерира устойчив на корозия съставен филм, за да се изолира корозивната среда и контакта с метала, за да се предотврати корозията на метала.
2.3 Неметален защитен слой: с бои, пластмаси, емайл и други материали, чрез боядисване и пръскане и други методи, за образуване на защитен филм върху повърхността на метала, така че металът и корозивните среди да се изолират, така че да се предотврати корозията на метала .
3. Повърхностна обработка на стомана
Преди обработката на стомана във фабриката, повърхността на компонентите неизбежно ще бъде оцветена с масло, влага, прах и други замърсители, както и наличието на грапавини, железен оксид, слой ръжда и други повърхностни дефекти. От предишните основни причини за корозия на стоманената конструкция знаем, че съдържанието на замърсители е важен фактор, влияещ върху степента на атмосферна корозия, а повърхностните замърсители ще повлияят сериозно на адхезията на покритията върху повърхността на стоманата и ще направят боята филмът под корозията продължава да се разширява, което води до повреда или повреда на покритието, което не може да постигне желания защитен ефект. Следователно, трябва да се подчертае качеството на повърхностната обработка на стоманата върху защитния ефект на покритието и живота на влиянието, понякога дори повече от самото покритие, разликите в производителността на въздействието на следните аспекти:
3.1. За носещите компоненти, които трудно се ремонтират по време на сервизния период, степента на отстраняване на накип трябва да се повиши по подходящ начин.
3.2. Преди и след отстраняването на котления камък трябва внимателно да се отстранят мазнините, неравностите, медицинската кожа, пръските и железният оксид.
3.3. качественото приемане на работите по отстраняване на накип и боядисване трябва да бъде в съответствие с нормативната уредба.
4.Антикорозионно покритие
Антикорозионните покрития обикновено се състоят от грунд и горно покритие. Грунд в прах повече, по-малко основен материал, филм груб, функцията на грунда е да направи филма боя с базовото ниво и горното покритие комбинация от твърдо вещество, тоест да има добра адхезия; грундът има инхибиращи корозията пигменти, може да предотврати появата на корозия, а някои също могат да бъдат пасивиране на метала и електрохимична защита, за да се предотврати ръждясването на метала. Горното покритие е по-малко прах, повече основен материал, след като филмът е лъскав, основната функция е да защити долния слой на грунда, така че трябва да е непропусклив за атмосферата и влажността и трябва да може да устои на физическото и химическо разлагане причинени от атмосферни влияния. Настоящата тенденция е да се използват синтетични смоли за подобряване на устойчивостта на средата на атмосферни влияния. Антикорозионните покрития с атмосферна устойчивост обикновено са устойчиви само на корозия на парна фаза в атмосферата. За места, подложени на корозия от киселини и основи и други среди, трябва да се използват покрития, устойчиви на киселини и основи.
Антикорозионната боя според защитната функция може да бъде разделена на грунд, средна боя и горно покритие, всеки слой боя има свои собствени характеристики, всеки отговаря за собствената си отговорност, комбинацията от слоевете, образуването на композитно покритие до подобряване на антикорозионните характеристики, удължаване на експлоатационния живот.
4.1 грундове
Грундовият слой, често използваните антикорозионни покрития са богат на цинк грунд и епоксиден желязочервен грунд, богатата на цинк боя се състои от голям брой микрофин цинков прах и малко количество филмообразуващи материали. Електрохимичните свойства на цинка са по-високи от тези на стоманата и когато е подложен на корозия, той има "саможертващ" ефект, така че стоманата е защитена. Корозионният продукт цинков оксид запълва порите и прави покритието по-плътно. Обикновено използваният богат на цинк грунд има следните три вида:
(1) водно стъкло неорганичен богат на цинк грунд, това е водно стъкло като основен материал, добавете цинков прах, смесване и четкане, след втвърдяване да се изплакне с вода, строителният процес е сложен, тежки условия на процеса, повърхностната обработка трябва да бъде в Sa2.5 или повече, в допълнение към температурата на околната среда, изискванията за влажност, образуването на покриващ филм е лесно за напукване, пилинг и рядко се използва.
(2) разтворим неорганичен богат на цинк грунд, грундът се основава на етил ортосиликат, алкохол като разтворител, частично хидролизирана полимеризация, добавете цинков прах, смесен с равномерно покритие.
(3) богат на цинк грунд, това е епоксидна смола като филмообразуващ основен материал, добавяне на цинков прах, втвърдяване за образуване на покритие. Богатият на цинк епоксиден грунд е не само отлични антикорозионни свойства и силна адхезия, а със следващото покритие епоксидната желязо-облачна боя е с добра адхезия. Използва се главно в общата атмосфера на конструкцията на стоманената рамка и корозията на нефтохимическото оборудване.
Червен грунд от епоксиден железен оксид е разделен на кутии с двукомпонентна боя, компонент А (боя), изработен от епоксидна смола, червен железен оксид и други антикорозионни пигменти, втвърдяващ агент, агент против потъване и др., Компонент Б е втвърдяващ агент, изграждането на пропорцията на разгръщането. Червеният железен оксид е вид физически пигмент против ръжда, неговата природа е стабилна, силна покривна способност, фини частици, може да играе добър екраниращ ефект във филма на боята, има добри характеристики против ръжда. Епоксидният железен оксид червен грунд върху стоманената плоча и горният слой епоксидна боя имат добра адхезия, бързо изсъхване при стайна температура, горният слой на повърхностната боя не кърви цвят, по-често се използва в стоманени тръбопроводи, резервоари, стоманени конструкции антикорозионни проекти , като грунд против ръжда.
4.2 среден слой боя
Средният слой боя обикновено е епоксидна слюда и епоксидна стъклена боя или епоксидна гъста суспензия. Епоксидната слюдена боя е направена от епоксидна смола като основен материал чрез добавяне на слюден железен оксид, микроструктурата на слюден железен оксид е като люспеста слюда, дебелината му е само няколко микрометра, а диаметърът му е от десетки микрометра до сто микрометра. Той е устойчив на висока температура, алкална устойчивост, киселинна устойчивост, нетоксичен, люспеста структура може да предотврати средно проникване, подобрена антикорозионна производителност и ниско свиване, грапавост на повърхността, е отличен среден слой антикорозионна боя. Епоксидната стъклена боя е епоксидна смола като основен материал, с люспеста стъклена скала като агрегат, плюс разнообразие от добавки, съставени от гъста антикорозионна боя тип гребло. Дебелината на скалата на стъклото е само 2 до 5 микрона. Тъй като люспите са подредени на слоеве над и под покритието, се образува уникална екранираща структура.
4.3 топ лак
Боите, използвани за покривни покрития, могат да бъдат разделени на три класа според техните ценови точки:
(1) Обикновеният клас е епоксидна боя, боя с хлориран каучук, хлоросулфониран полиетилен и т.н.;
(2) Средният клас е полиуретанова боя;
(3) По-висок клас е силикон-модифицирана полиуретанова боя, силикон-модифициран акрилен горен слой, флуорна боя и т.н.
Епоксидна боя след химическо втвърдяване, химическа стабилност, плътно покритие, силна адхезия, високи механични свойства, устойчива е на киселина, основи, сол, може да устои на корозия на различни химически среди.
5. Изборът на антикорозионна боя трябва да вземе предвид няколко точки
5.1 Трябва да се обърне внимание на последователността на условията на използване на конструкцията и гамата от избрани бои, въз основа на корозивната среда (вид, температура и концентрация), газова фаза или течна фаза, горещи и влажни зони или сухи зони и други условия за подбор. За киселинна среда може да се използва боя с фенолна смола с по-добра киселинна устойчивост, докато за алкална среда трябва да се използва боя с епоксидна смола с по-добра алкална устойчивост.
5.2 Трябва да се вземат предвид възможностите за строителни условия. Някои са подходящи за четкане, други за пръскане, трети за естествено сушене, за да се образува филм и т.н. За общи условия е препоръчително да използвате суха, лесна за пръскане боя със студено втвърдяване.
5.3 Помислете за правилното съвпадение на покритията. Тъй като по-голямата част от боята е органичен колоиден материал като основен материал, боядисвайте всеки слой филм, неизбежно има много изключително малки микропорести, корозивни среди все още могат да проникнат през ерозията на стоманата. Следователно конструкцията на сегашната боя не е с еднослойно покритие, а с многослойно покритие, като целта е да се намалят микропорите до минимум. Трябва да има добра адаптивност между грунд и горно покритие. Като боя с винилхлорид и фосфатиращ грунд или желязочервен алкиден грунд, който поддържа използването на добри резултати и не може да се използва с грунд на маслена основа (като червена боя на маслена основа), поддържащ употребата. Тъй като перхлоретиленовата боя съдържа силни разтворители, ще разруши грундиращия филм.
От голямо значение е да се свърши добра работа в областта на защитата от ръжда и корозията, за да се насърчи развитието на строителството на стоманени конструкции, да се спестят материали, да се удължи експлоатационният живот на сградата, да се осигури безопасно производство и да се намали замърсяването на околната среда.
№ 568, първокласен път на Янкинг, High-Tech Zone Jimo, град Qingdao, провинция Шандонг, Китай
Copyright © 2024 Qingdao Eihe Steel Strection Group Co., Ltd. Всички права запазени.
Links | Sitemap | RSS | XML | Privacy Policy |
Teams